Investment casting and sand casting are two different methods of metal casting, both of which involve pouring liquid metal into a mold to create a metal part. Investment casting and sand casting have their own advantages, so you can’t simply say which one is better, but which one is more suitable for producing your products. As a professional investment casting foundry, the difference between investment casting and sand casting are often asked by our customers, so we wrote this article to compare two casting methods.
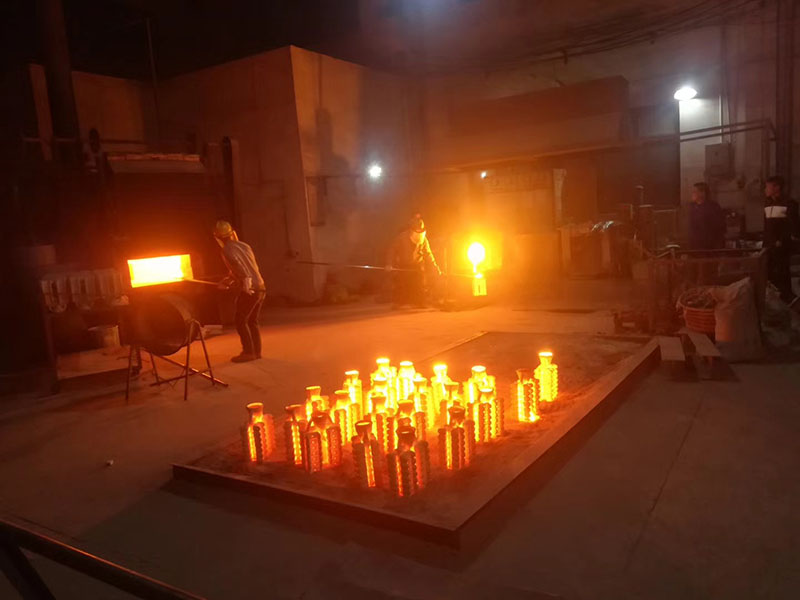
Investment casting is a precision casting process that uses a lost wax process to shape the metal into a component. Firstly, we have to make a set of molds, lost wax casting molds are usually made of aluminum, if quantity of the component is large, we will also use steel molds. The process of investment casting, also known as lost wax casting, we inject wax into the mold to produce a wax pattern, and the wax patterns are assembled onto a sprue (what we called a “tree”), and then wrapped in refractory slurry on the outside of the tree to make a ceramic shell. Pour the molten metal into the shell. After cooling, we get the metal castings. Investment casting has the following advantages:
- Investment casting can produce parts with complex shapes with very thin walls.
- High accurate, investment castings can achieve high dimensional tolerance request.
- Smooth surface finish can save further machining or surface finish process.
- Material of investment casting can be Ferrous, nonferrous or duplex alloys. Investment casting can be quite economical by repeat runs.
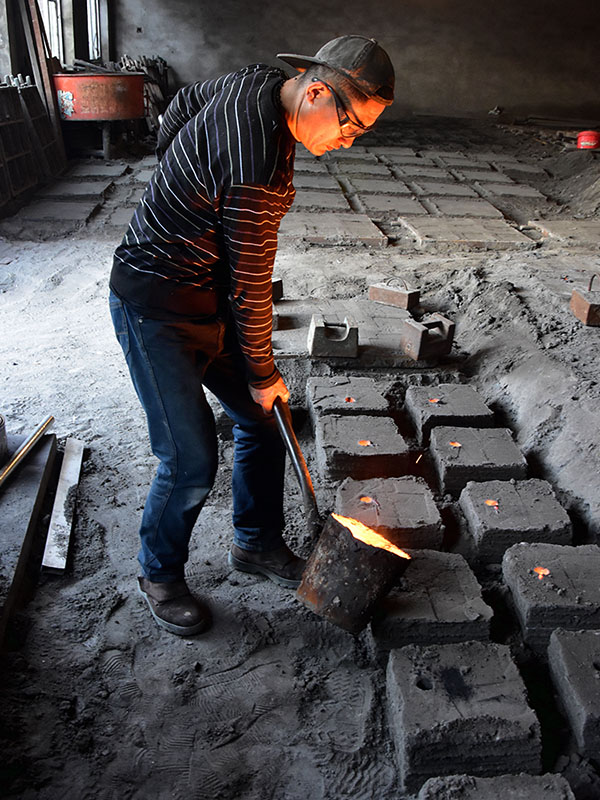
Sand casting uses sand to form the mold surface. The mold made of sand has some flexibility, so when the liquid metal cools and hardens, there are fewer cracks, tears or other types of defects. Sand casting has the following advantages:
- The cost of sand casting is lower especially in shorter runs.
- Sand casting can produce larger castings.
- Ferrous and non-ferrous metals can be also used.
- Post-cast tooling cost is lower.
Differences Between Investment Casting & Sand Casting
Production design: In investment casting, ceramic shell is formed from liquid slurry, so investment castings can be designed into almost any shape, and engineers have great freedom to add the complex structures and shapes required in the design. In sand casting, the product is often designed to be tapered, so sand casting parts can be taken out from the sand mold easily with less friction. Sand castings with internal cavities or voids are more difficult to make. Sand castings requires insertion of a suitable core into the mold to form the internal structure, sometimes multiple cores may be needed.
Weight: Investment casting can make castings in weight less than 450 grams, while sand casting cannot cast small pieces with complex structures.
Surface finish: The surface of investment casting and sand casting has a big difference. Because of the material of the mold, the surface of the investment casting parts is smooth and can achieve high tolerance requirements. After removing the gate and blasting, the castings can be used directly. In sand casting, the mold has to be split apart to release the castings, so the parting line is more obvious. And because the sand is rough, the surface is also relatively rough and requires additional time and cost to process.
Cost: The complexity and preparation process of the investment casting process makes it cost more than sand casting. Comprehensively speaking, investment casting method is usually superior to other casting methods, especially in product details and surface finish. Shanghai Heda Castings Co., Ltd, a professional precision foundry with nearly 20 years of experience, is ISO-9001 certified. We can provide one-stop solution for your investment casting parts, from mold design to finished castings, machined castings, as well as heat treatment and surface treatment if requested. Please feel free to contact us if you need any assistance with your investment castings.