Investment casting is also known as “lost wax casting”, it has been used for metal-forming for almost 5,000 years. Today it is still one of the most used manufacturing methods to produce a great variety of components for a wide range of industries. Heda castings produces high quality investment casting parts by carrying out the following procedures.
STAGE 1
A well-designed injection mold with one or multi cavities is the first step of casting high quality investment castings, it can be made of aluminium which is more economical to make and easily modified if changes are required, or an automatic mold made of steel for mass production. The injection mold is used to make wax patterns of required casting parts, it is made by CNC machining center.
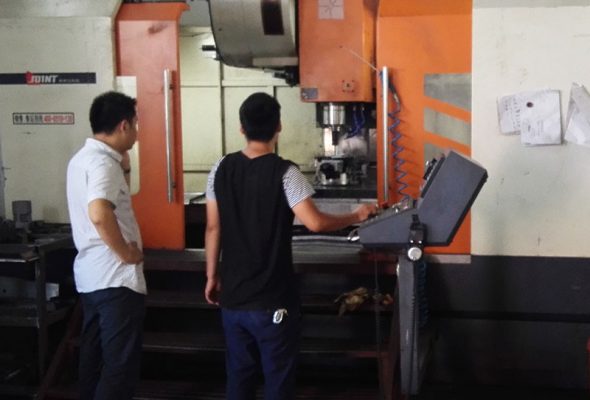
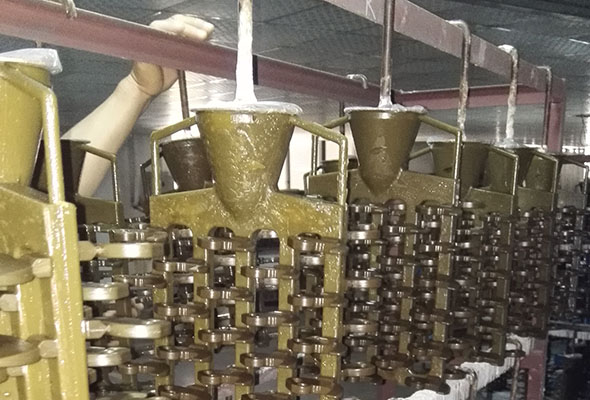
STAGE 2
Wax patterns of required casting parts are made by injecting wax into the mold, after repairing the wax patterns (such as removing burrs or parting line), the wax patterns are assembled onto a sprue, each sprue or “tree” may have just one large pattern or many small patterns.
STAGE 3
This stage is call shell building or coating. The wax pattern assemblies are dipped into a fine ceramic slurry, then larger particles of ceramic are poured onto the surface. This coating process needs to be repeated several times to build up a shell in a required thickness and strength. Then investment molds are left to dry completely.
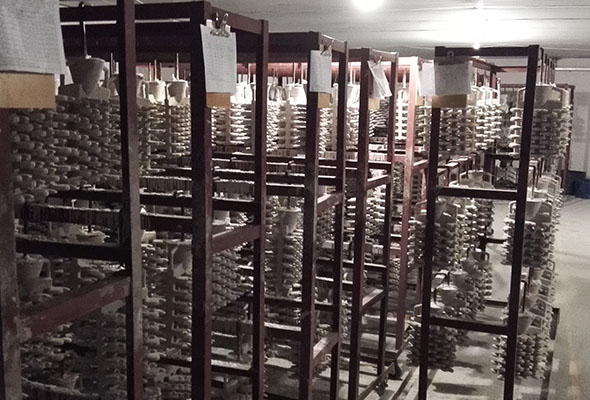
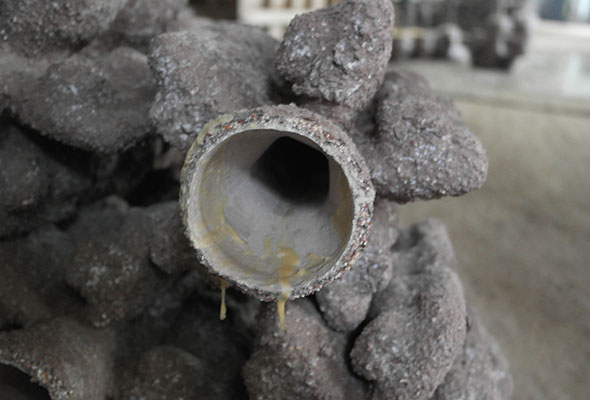
STAGE 4
Once the shell mold is dried, it is placed in a steam autoclave so the wax is melted and flow out from the mold, this is the “dewax” process or “lost wax” process in investment casting. The shell mold is fired at over 1000°C to burn out any remaining wax pattern material and to strengthen the mold.
STAGE 5
After dewax process, molten metal is poured into the mold. When the metal is cooled and solidified, the ceramic shell is broken away and the castings can be cut away from the sprue, then excess metal is ground off carefully from required casting part.
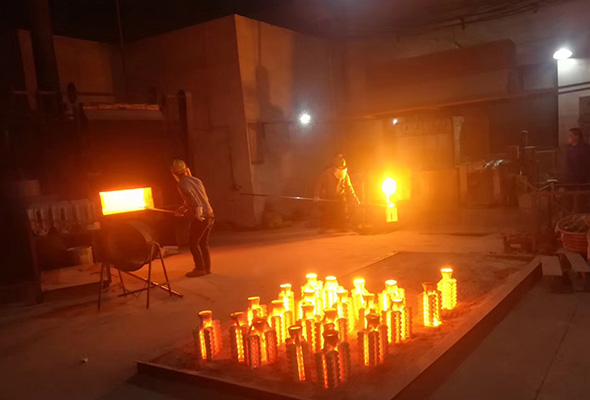
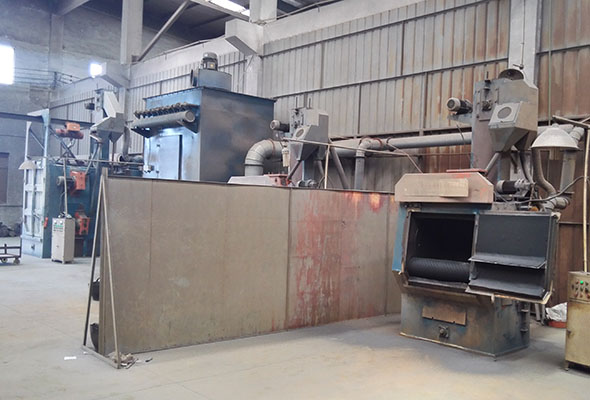
STAGE 6
Once we have the casting parts, heat treatment can be performed to improve the mechanical properties of casting parts. Shot-blasting or sand-blasting can remove scales, burrs and achieve smoother surface finish. Machining process can also be done in our foundry, including grinding, drilling, broaching, milling and so forth. Surface treatment is normally the last step of investment casting, such as mirror polishing, galvanizing, chrome plating and so on.
STAGE 7
We can do 100% strict inspection according to the drawings of our products, as well as material testing, hardness testing, x-ray, dye penetrant testing if needed, inspection report can be provided together with shipping documents. Finished casting parts are packed in standard exporting crates and custom packages are also available.
